Kiel Canal Lock Chamber
A new bypass for one of the world‘s most important shipping lanes: a fifth lock chamber is being built – right between the two already existing locks at the western end of the Kiel Canal. The job calls for high precision and the right concrete mix.
The Kiel Canal is one of the most travelled man-made shipping lanes worldwide. At Brunsbüttel, two dual-chambered locks serve to raise and lower ships on the water between the river Elbe and the Baltic Sea. But, these aging locks are in urgent need of maintenance and repair – a project that will take years to complete. And, any slowdown or stoppage at this key junction point is simply unthinkable. Thus, a bypass is being built at the site, in the form of a fifth lock chamber. The project is taking place on the island between the "small" and "big" lock. The job calls for precision work, as to avoid any disruptions or, worse, damage to the existing locks on either side. Any shocks or tremors must be avoided.
Consequently, preparation of the new site did not begin as usual, with sinking of sheet piling with vibro machines or pile drivers. Instead, diaphragm walls were constructed using a special method for the building of locks and waterside walls that keeps ground shocks to a minimum. Prior to installation, a special digger was used to clear a 1.20 m x 8 m trench (in three shovel loads) to a depth of up to 40 m. At the same time an argillaceous suspension, the clay mineral (bentonite), was pumped for stability into the resulting shaft. This prevented cave-ins while the diaphragm slats were inserted. Highly precise work was a must to ensure that the overlapping slats created a perfectly plumb, gap-free wall.
When the shaft had been dug to the desired depth, a special cement was added to the suspension for concreting the bottom. 40-tonne pilings were lowered. Through progressive introduction of more cement into the suspension, a mix was created in the shaft, which, when hardened, provided strong support for the piling wall. Special measurement equipment and continuous monitoring of impacts on the neighbouring locks ensured maximum safety at the site.
An innovative approach has also been used for anchoring of the lock basin to the bed of the waterway – in order to keep shocks to an absolute minimum: concrete expansion anchors are being installed diagonally using high pressure injection (HPI) drilling to first create a 244 millimetre hole 30 to 40 metres deep in the ground. Then, the HPI drill injects a cement suspension at a pressure of nearly 400 bar into the surrounding earth. This erodes away soil and replaces it with cement – all precisely controlled by computer. The high pressure injection valves cut through the overburden, so that the suspension is mixed in with the native soil – which in Brunsbüttel consists mostly of sand and gravel – creating a concrete anchor roughly seven meters long with a diameter of 1.10 metres. Prior to hardening, ribbed steel reinforcement rods are inserted and the drill hole filled with a special cement suspension.
As many as 1,690 such anchors are planned for the lock basin. And because it is meant to last for at least the next 100 years, the Federal Waterways Engineering and Research Institute (Bundesanstalt für Wasserbau – BAW) has imposed high geometric and material standards on the project. To ensure that these requirements would be met, the construction consortium thoroughly tested the anchor making process prior to the start of building. Site manager Sebastian Grote explains: "There is no standard solution for a project like this. Throughout the testing, we adjusted parameters such as pump pressure, pumped volume, drilling and transport speeds in close coordination with BAW and the maritime affairs office, in order to ensure that the necessary standards of quality and stability are met.”
The bypass is to be ready, the fifth lock chamber completed, within five years. And, at a length of 350 m, it will be a full 20 m longer than the current “big” lock. This will make it possible for even larger ships to take advantage of the well-travelled shortcut through the canal.
HeidelbergCement supplies several CEM III cement types, in total about 35,000 tonnes, and about 15,000 tonnes diaphragm wall suspension for this project.
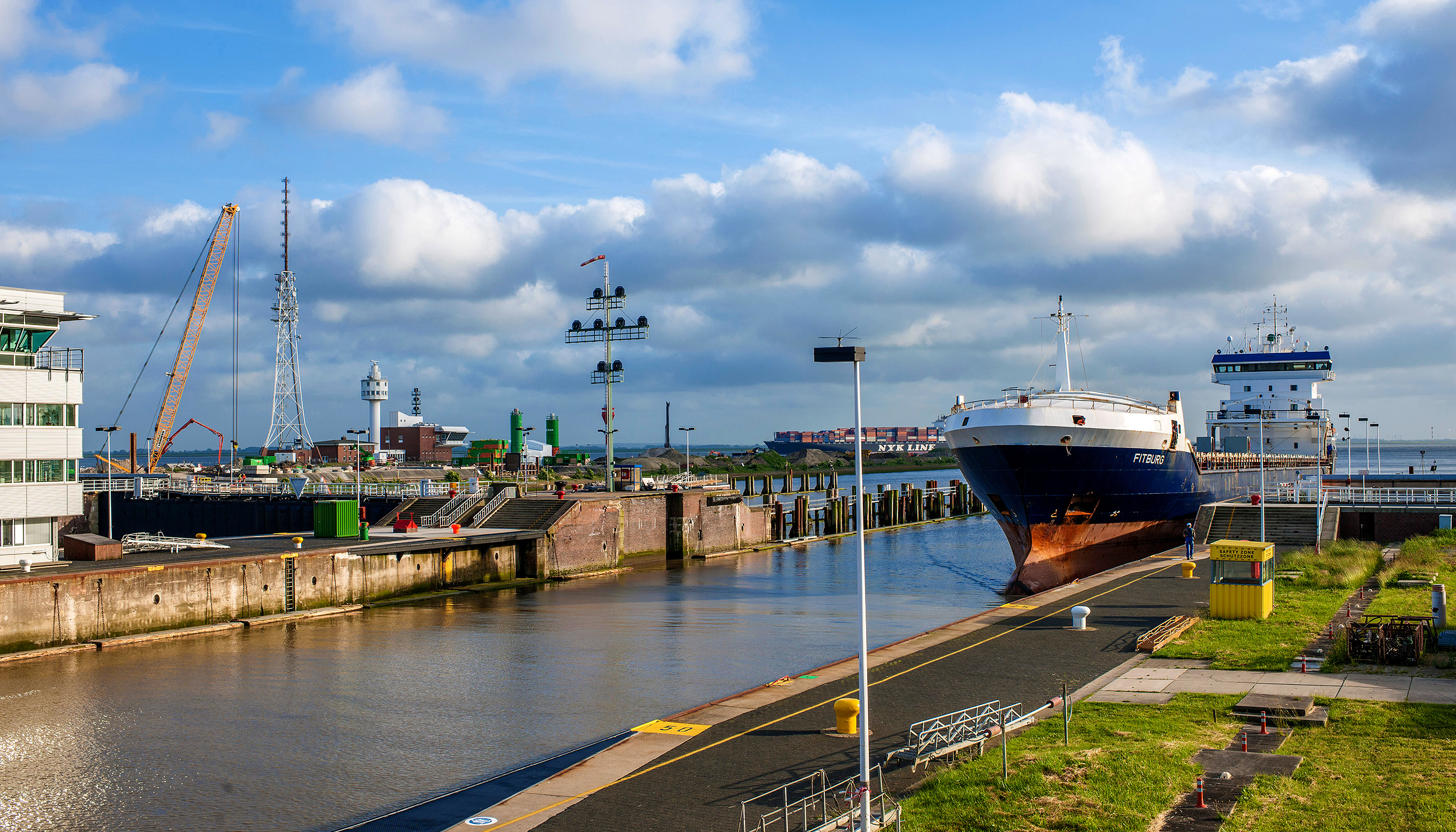
Kiel Canal Lock Chamber, Germany. At a length of 350 m, it will be a full 20 m longer than the current “big” lock.
HeidelbergCement / Steffen Fuchs
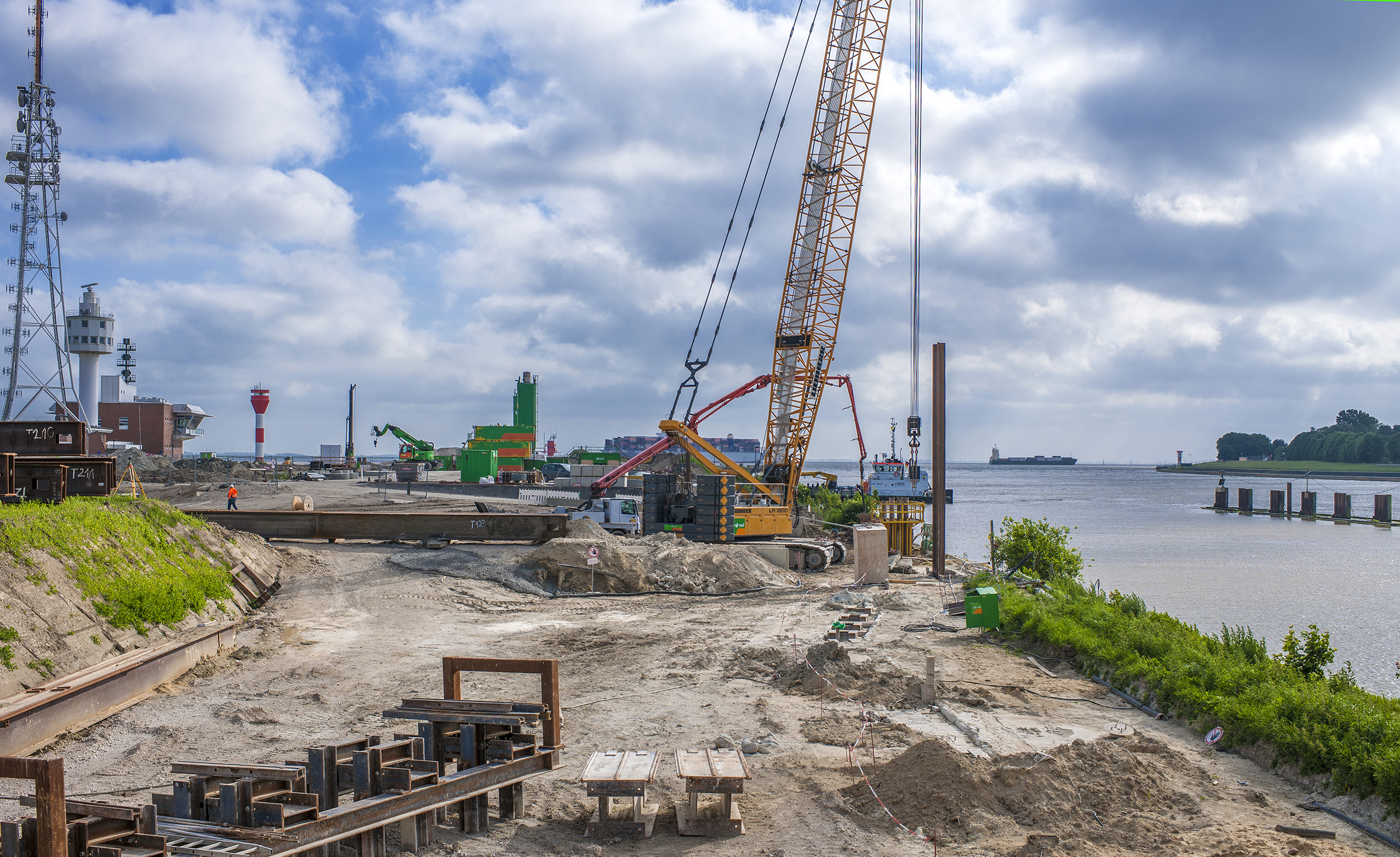
Kiel Canal Lock Chamber, Germany. At a length of 350 m, it will be a full 20 m longer than the current “big” lock.
HeidelbergCement / Steffen Fuchs

Kiel Canal Lock Chamber, Germany. At a length of 350 m, it will be a full 20 m longer than the current “big” lock.
HeidelbergCement / Steffen Fuchs
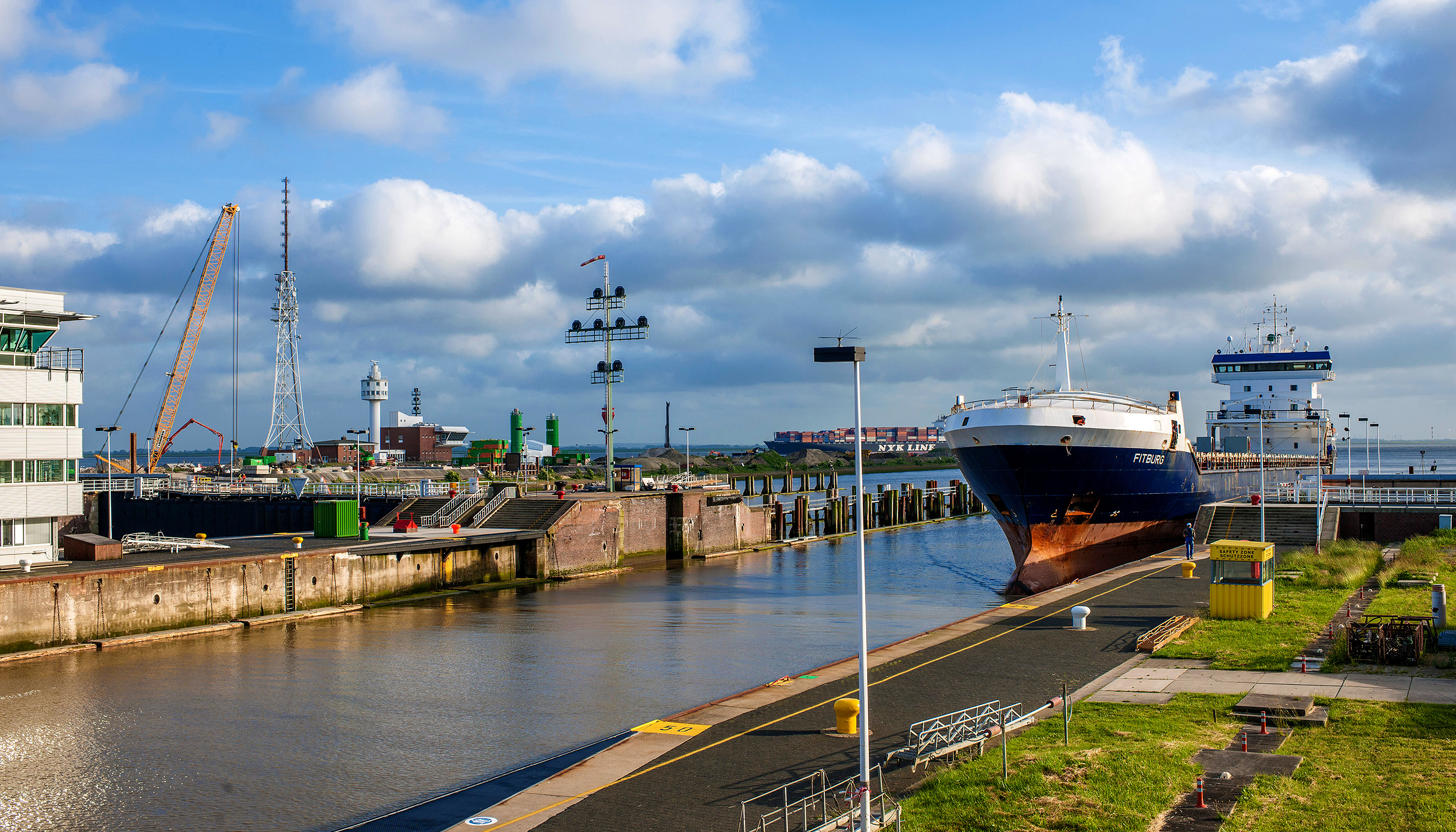
Kiel Canal Lock Chamber, Germany. At a length of 350 m, it will be a full 20 m longer than the current “big” lock.
HeidelbergCement / Steffen Fuchs
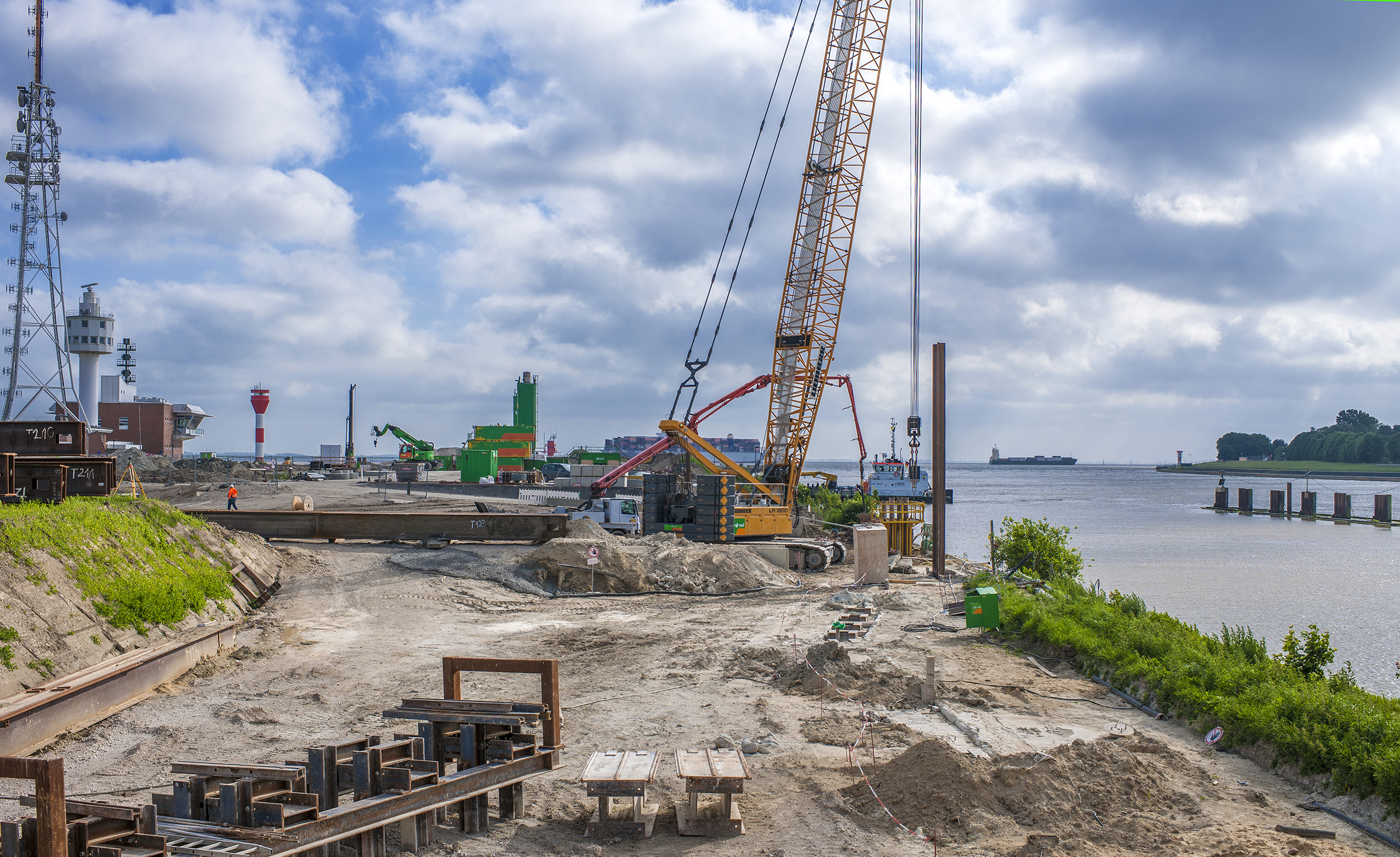
Kiel Canal Lock Chamber, Germany. At a length of 350 m, it will be a full 20 m longer than the current “big” lock.
HeidelbergCement / Steffen Fuchs

Kiel Canal Lock Chamber, Germany. At a length of 350 m, it will be a full 20 m longer than the current “big” lock.
HeidelbergCement / Steffen Fuchs