„SAVE CO₂“ – Wir sind dabei!
Im Rahmen des Forschungsprojekts „SAVE CO₂“ haben sich Heidelberg Materials, ThyssenKrupp Steel, das Institut für Technologie der Metalle der Universität Duisburg-Essen und das Nachhaltigkeitsforschungsinstitut Fraunhofer UMSICHT zusammengeschlossen. Unser gemeinsames Ziel ist es, neuartige Elektroofenschlacken der Stahl- und Eisenindustrie als Rohstoffe in der Herstellung von Zement und Beton einzusetzen. Das Projekt startete im Mai 2021 und wird die kommenden vier Jahre durch das FEhS - Institut für Baustoff-Forschung e. V. geleitet.
Gemeinsam geht es besser – Stahl- und Zementindustrie
Die Stahl- und die Zementindustrie arbeiten seit jeher eng zusammen. Dadurch entstehen Synergien, die Ressourcen schonen und die Entstehung von Treibhausgasen in der Atmosphäre verhindern. Die Nebenprodukte aus der Eisen- und Stahlproduktion führen in der Bauindustrie zu einem minimierten Verbrauch wertvoller Rohstoffe und geringerem CO₂-Ausstoß.
Beispielsweise bildet langsam, luftgekühlte Hochofenschlacke ein steinartiges Material, das schon lange als Zuschlagstoff in der Betonherstellung verwendet wird. Durch die heute übliche Wassergranulation von Hochofenschlacke entsteht glasiger und hoch reaktiver Hüttensand als neues Produkt. Auf Grund von dessen hoher Reaktivität und anderen positiven Eigenschaften kann dieser als Zementbestandteil verwendet werden und einen Teil des Portlandzementklinkers ersetzen.
Beide Anwendungen verringern die Emissionen und schonen Ressourcen – insbesondere natürlichen Kalkstein, Sand und Kies.
Ein neuer Ansatz
Die Stahlindustrie befindet sich derzeit in einem Strukturwandel. Das klassische Hochofenverfahren hat ausgedient. Folglich steht jedoch auch immer weniger Hüttensand als Klinkerersatz für die Zementindustrie zur Verfügung.
Die Dekarbonisierung der Stahlproduktion: Die Direktreduktion von Eisenerz zu Eisenschwamm (Direct Reduced Iron – DRI) wird die klassische Roheisenproduktion über den Hochofenprozess ersetzen. Hierbei kann neben der direkten Energieeinsparung auch grüner Wasserstoff Kohlestaub als Reduktionsmittel ersetzen. DRI kann dann z. B. in einem Elektrolichtbogenofen zu Rohstahl aufgeschmolzen werden. Durch diese neuen Prozessrouten werden die CO₂-Emissionen erheblich reduziert. Obwohl bei den neuen DRI-Verfahren auch Schlacken als Nebenprodukte anfallen, unterscheiden sich diese in deren chemischer und mineralogischer Zusammensetzungen von Hüttensand. Dementsprechend können diese neuartigen Schlacken nicht eins zu eins von der Zementindustrie verwendet werden. Aber zum Glück ist das nicht das Ende der Geschichte!
Ein weiteres „Material to Build our Future“
Ein Hauptziel des SAVE-CO₂-Projekts besteht darin, industrieübergreifende Synergien zu sichern: Die chemische und mineralogische Zusammensetzung der DRI-basierten Schlacken soll gezielt eingestellt werden, um denen von Hüttensanden zu entsprechen. Wir gehen davon aus, dass solch optimierte Elektroofenschlacken eine weitere Klinkerersatz-Quelle für die Zementindustrie sein werden, um auch zukünftig CO₂ einzusparen.
Gleichzeitig wird durch das Upcycling dieses neuen Stahlnebenprodukts eine mögliche Deponierung der Schlacken vermieden. Die fünf Projektpartner repräsentieren die gesamte Wertschöpfungskette, von der Prozessentwicklung, zur Produktion von DRI, Stahl und der Schlacke, bis hin zur Verwendung der Schlacke in Zement und Beton. Mit diesem Pionierprojekt und ganz im Rahmen der Kreislaufwirtschaft schaffen wir einen Mehrwert für die Gesellschaft, die Umwelt und die beteiligten Projektpartner. Gleichzeitig stärken wir die bestehenden Synergien zwischen der Zement- und der Stahlindustrie weiter.
Unser Forschungs- und Entwicklungsteam ist stolz darauf, Teil des SAVE-CO₂-Projekts zu sein und ein weiteres „Material to Build our Future“ zu entwickeln.
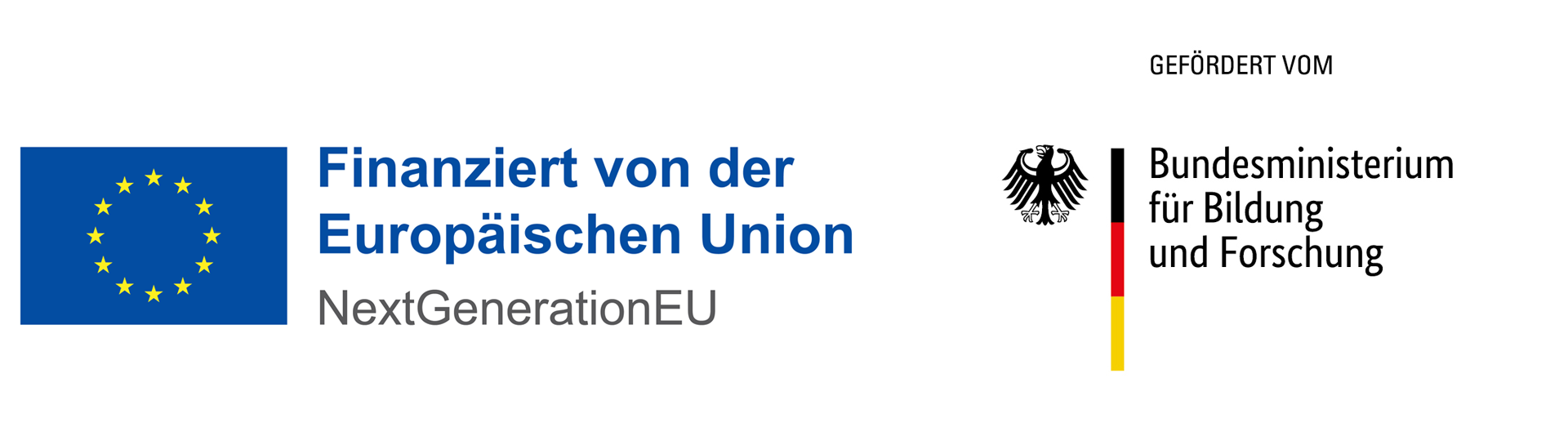
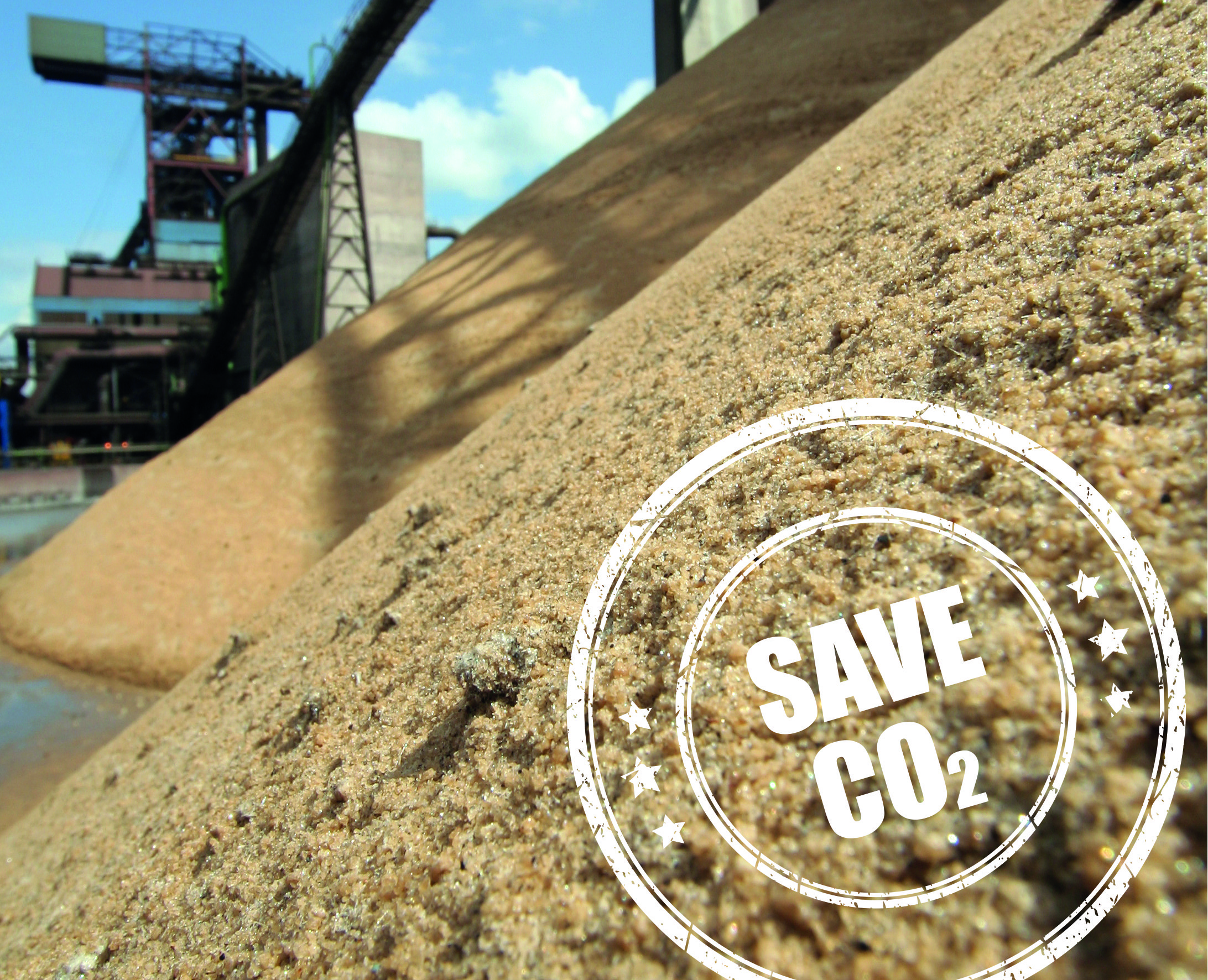
Save CO₂.
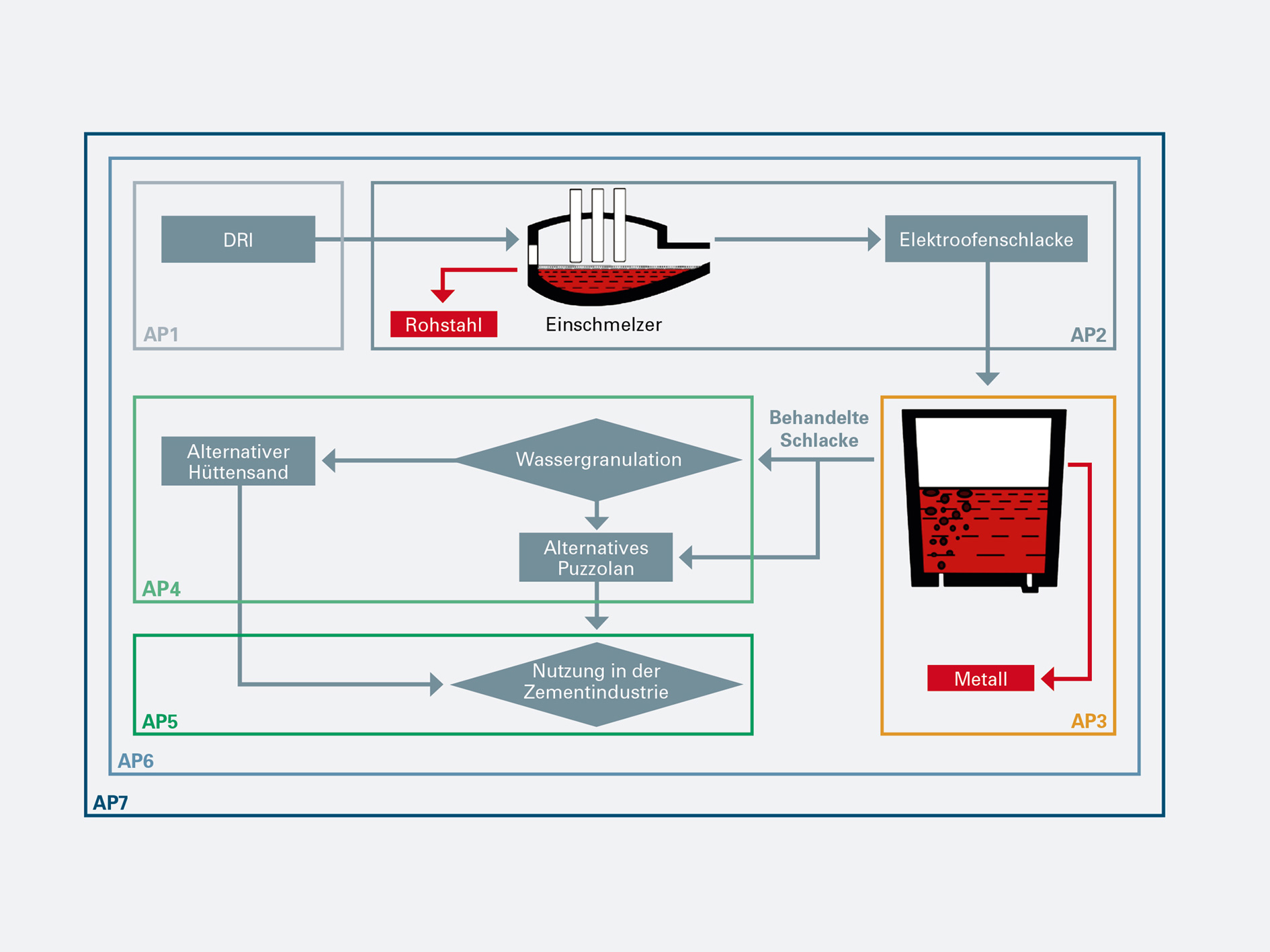
Schematische Darstellung der Arbeitspakete und der beteiligten Partner. AP1: Erzeugung von verschiedenen DRI-Qualitäten und Metallanalytik
AP2: Schmelzprozess im Elektroofen
AP3: Chemische Behandlung der Elektroofenschlacke zur weiteren Transformation (ggfs. mit Eisenrückgewinnung)
AP4: Erzeugung und Charakterisierung eines latent hydraulischen und puzzolanischen Materials
AP5: Einsatz der gemahlenen Schlacken zur Erzeugung von Portlandkompositzementen in Anlehnung an DIN EN 197-1
AP6: Ökologische und ökonomische Prozessbewertung
AP7: Projektmanagement und Dokumentation
D. Algermissen, FEhS Institut
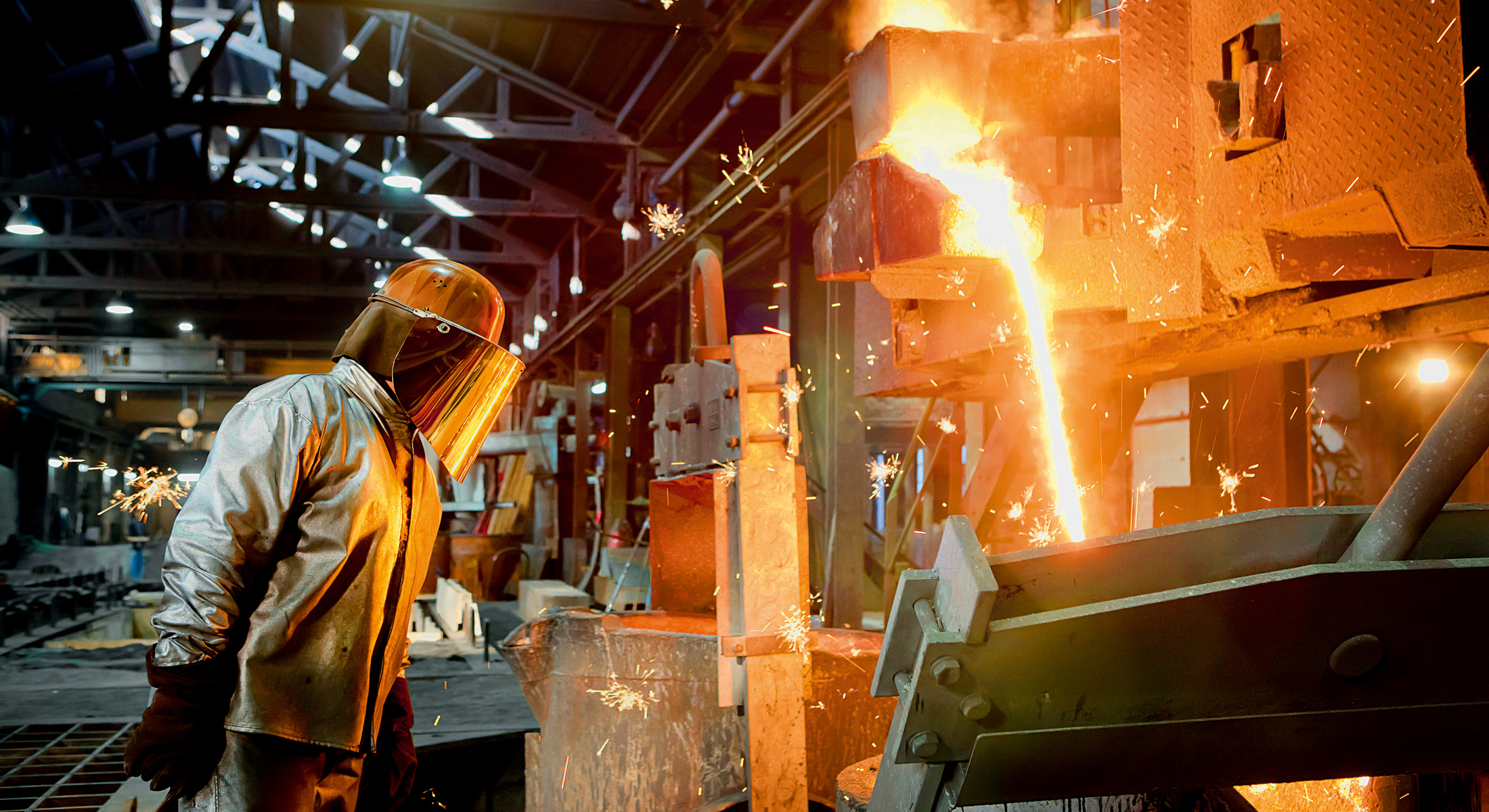
Blast furnace.
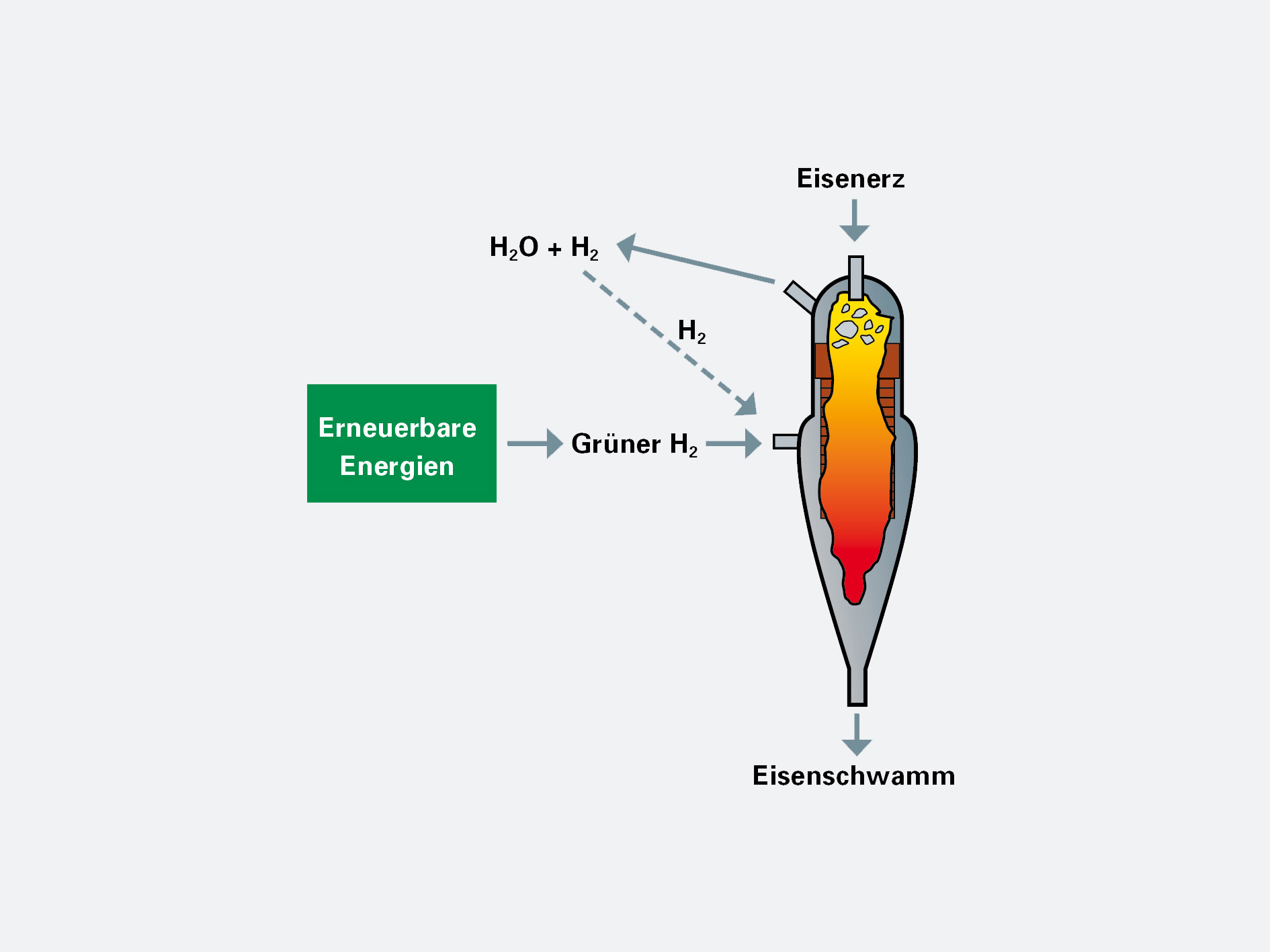
Direktreduktion von Eisenerz zu Eisenschwamm.
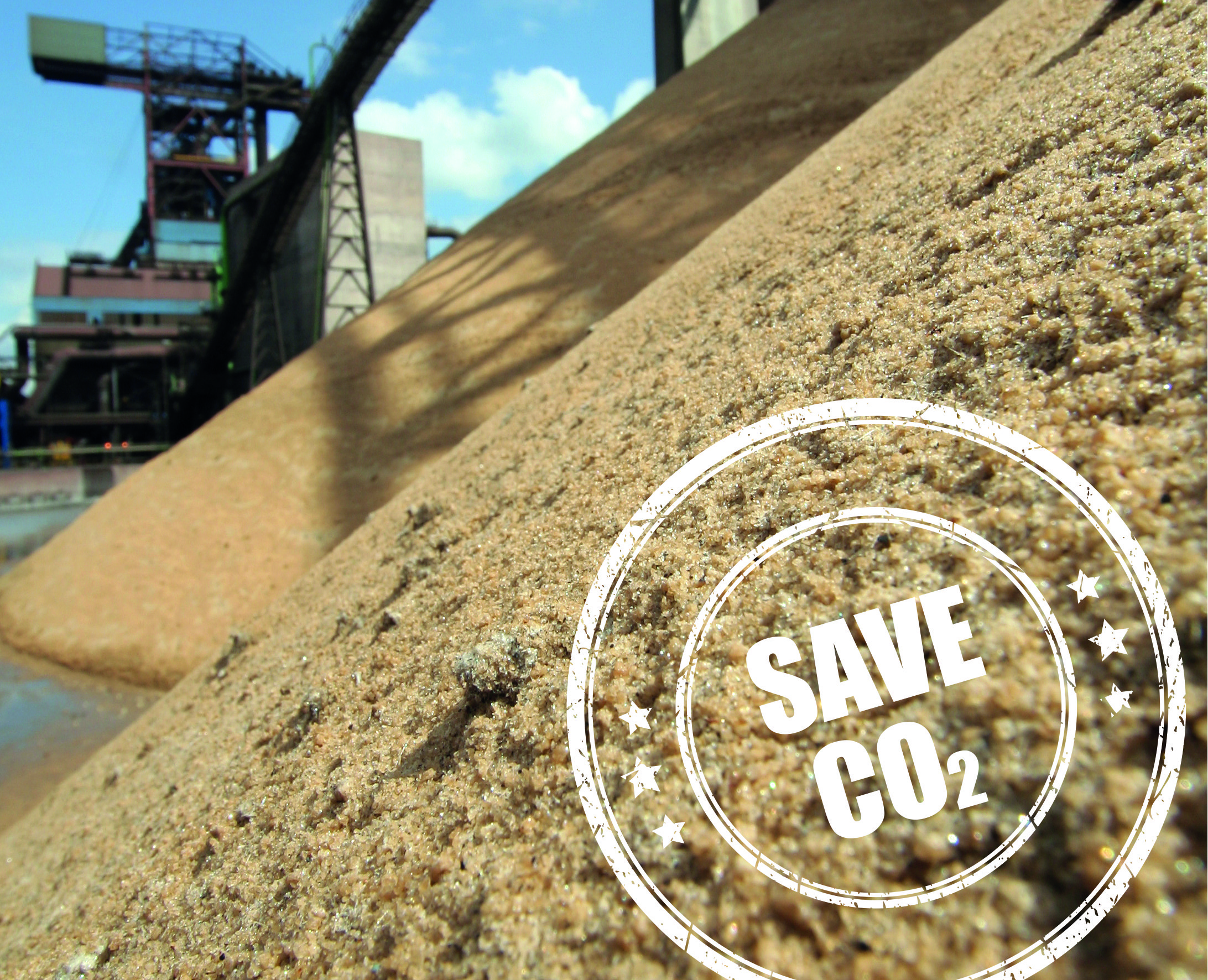
Save CO₂.
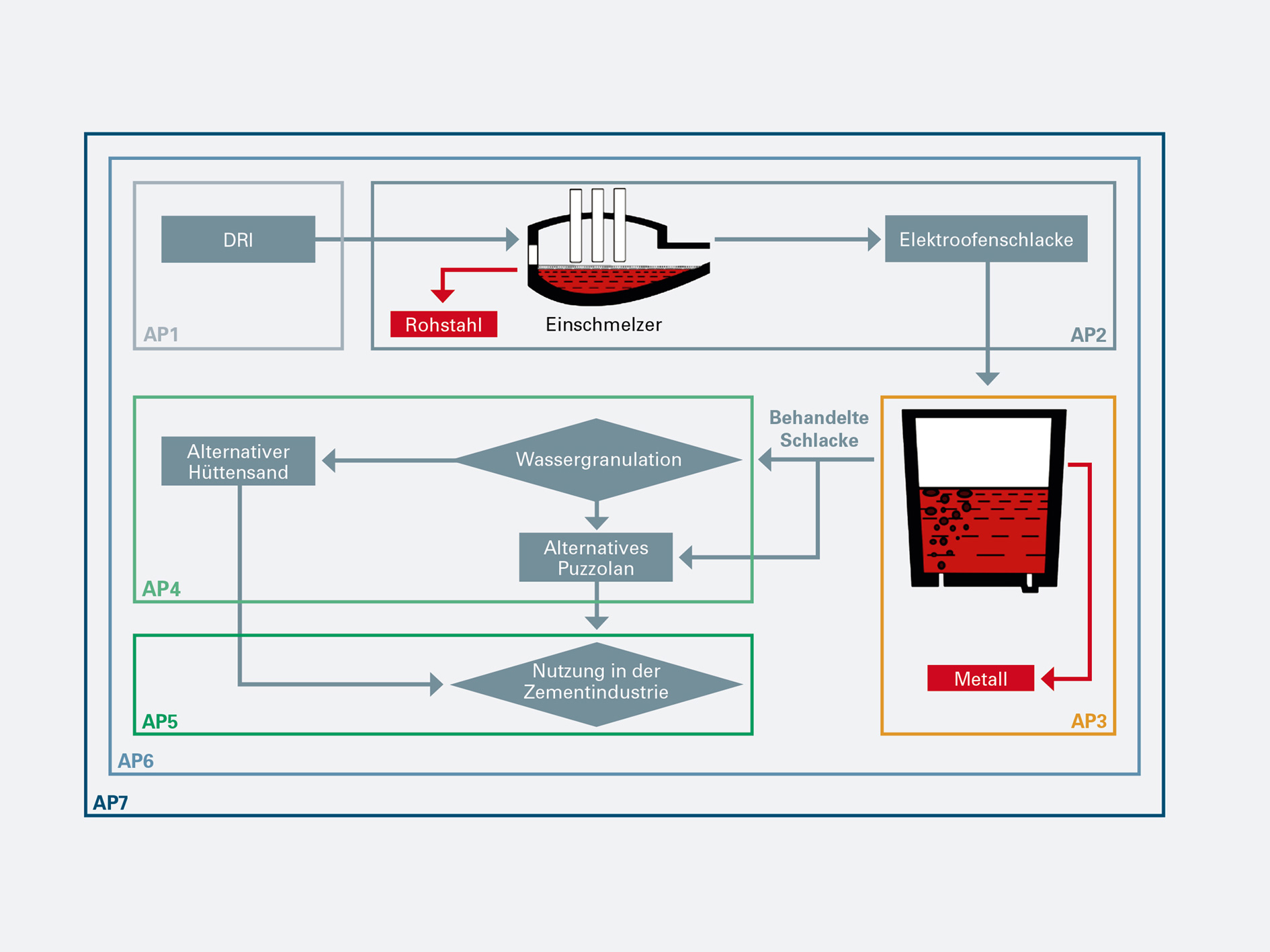
Schematische Darstellung der Arbeitspakete und der beteiligten Partner. AP1: Erzeugung von verschiedenen DRI-Qualitäten und Metallanalytik
AP2: Schmelzprozess im Elektroofen
AP3: Chemische Behandlung der Elektroofenschlacke zur weiteren Transformation (ggfs. mit Eisenrückgewinnung)
AP4: Erzeugung und Charakterisierung eines latent hydraulischen und puzzolanischen Materials
AP5: Einsatz der gemahlenen Schlacken zur Erzeugung von Portlandkompositzementen in Anlehnung an DIN EN 197-1
AP6: Ökologische und ökonomische Prozessbewertung
AP7: Projektmanagement und Dokumentation
D. Algermissen, FEhS Institut
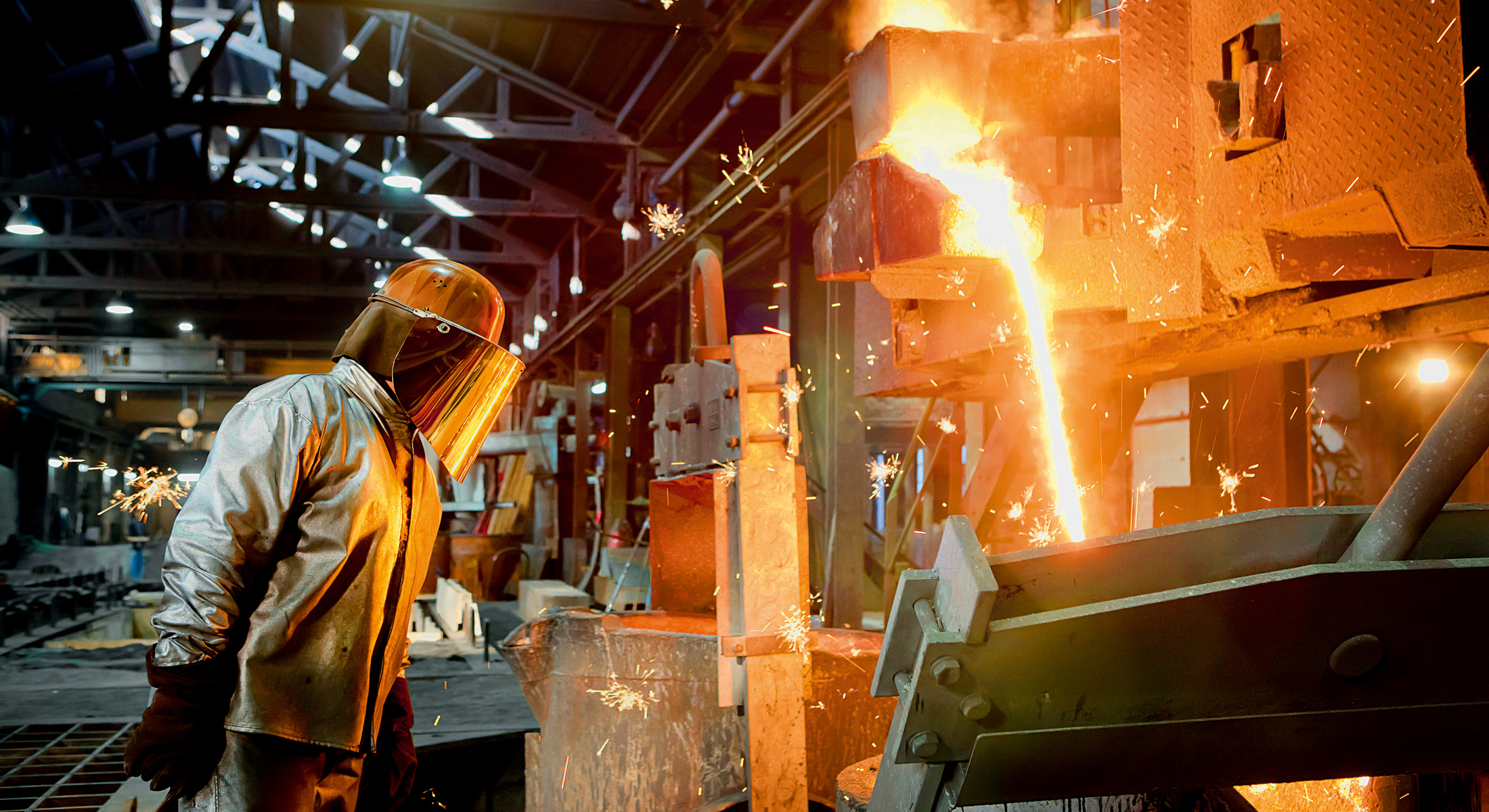
Blast furnace.
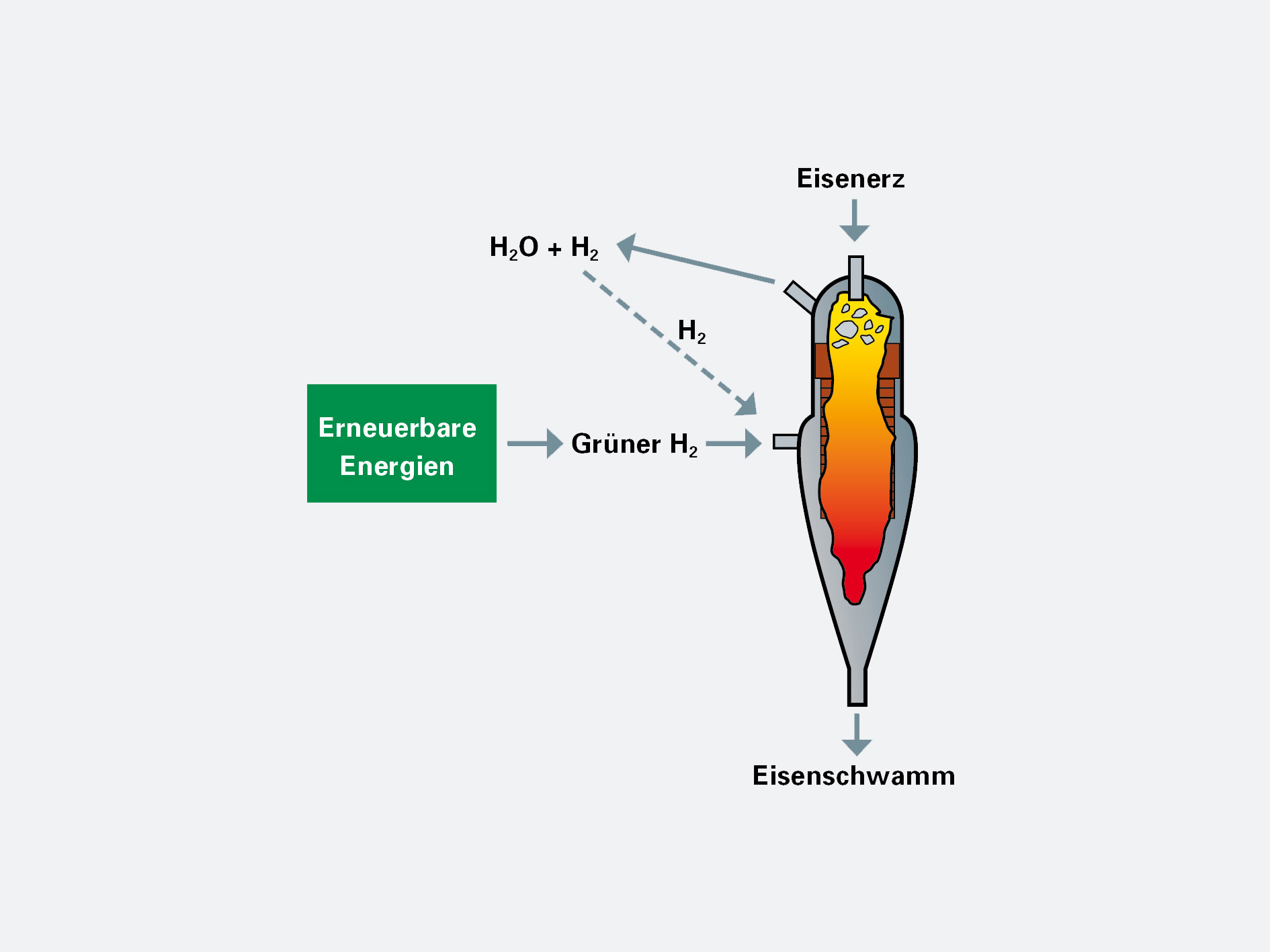
Direktreduktion von Eisenerz zu Eisenschwamm.